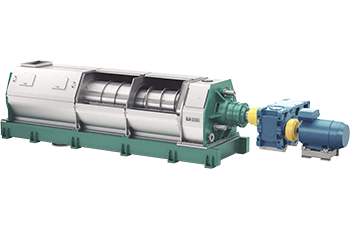
Screw press
Dewatering is made to thicken the pulp consistency from as low as 3% and up to 35%. A high consistency pulp entering the heating zone will ensure a low steam consumption, and a better dispersion result.
As the most advanced system the HDS produces the best dispersing results. It is also the most flexible system, with optional features such as in-line bleaching. The key feature of hot dispersing is treatment with high temperature at high pulp consistency. This leads to many advantages: improvement of fiber properties, reduction of bacteria, and softening of dirt and tacky contaminants for a more efficient dispersing. Retention time is 2 minutes at a temperature of up to 120°C (248°F).
The system is further described below – with all the treatment steps for dewatering, heating, dispersing and bleaching.
Dewatering is made to thicken the pulp consistency from as low as 3% and up to 35%. A high consistency pulp entering the heating zone will ensure a low steam consumption, and a better dispersion result.
The heating zone is sealed by a plug screw, in order to achieve a low steam consumption and flexible operating temperatures. Shear forces introduced by the plug screw creates a pre-dispersing effect.
Before heating begins, the pulp is shredded into fine pieces. A fine and uniform pulp ensures that all fibers and contaminants reach the required temperature in the pre-heater.
The pulp is heated to a uniform temperature of 90-120°C, depending on raw material. Wax, hot melts and stickies reach their melting point so that the contaminants’ strength properties are weakened.
The infeeder feeds the pulp from the pre-heater to the disperser. The infeed zone of the disperser has patented features that decreases risk of blocking, and contributes to a low energy consumption.
The fibers pass through a narrow gap between rotating discs, where any impurities are disintegrated to an invisible size. The devil-tooth pattern of the discs is optimized for each pulp mixture in order to achieve a gentle treatment of the fibers. Adjustment of the disc gap can be done on-line with an accuracy of 0,01 mm.
A discharge plug screw at the outlet of the disperser is an optional feature that enables high consistency discharges of up to 35%.
The Grubbens pump is suitable for use directly after the disperser. This solution is optimal for medium consistency discharges of 8-12%.
Chemicals for pre-bleaching are added at the first plug screw. Bleaching is done in the heating zone where the pulp is under pressure and at high consistency. This leads to minimum dilution effect, low use of chemicals, and low energy consumption.
Chemical post-bleaching is done at the disperser. The process with both pre-bleaching and post-bleaching means that different temperatures, pulp consistencies and chemical types can be used in the two steps.
Test your material in our pilot plant and analyze machine performance in our lab!
Download InfoCustomized designs for your unique application.
Full service on site with your machine delivery.
We have offices in Sweden, Canada, Germany, China, and agents all over the world.
Let us visit your plant and help you improve performance!
Download InfoAre you in need of technical support or wear parts for your machine? Interested in a visit from our staff or a project quotation? Please contact one of our local offices around the world!
Johan Göth
Niklas Tunell
Christian Stiller
Åsa Billfeldt
Gith Cedulf
Stefan Virtanen
Tomas Anarp
Kevin Klassen
Frank Jiang
Kent Xu
Tony Lu
Cellwood Machinery